Процесс переработки нефти можно разделить на 3 основных этапа:
1. Разделение сырья на фракции, различающиеся по интервалам температур кипения (первичная переработка);
2. Переработка полученных фракций путем химических превращений содержащихся в них углеводородов (вторичная переработка);
3. Смешение компонентов с получением товарных нефтепродуктов с заданными показателями качества (товарное производство).
Функциональной единицей нефтеперерабатывающего завода является технологическая установка — производственный объект с набором оборудования, позволяющего осуществить определённый технологический процесс.
Нефть, поставляемая на завод, вначале поступает на ЭЛОУ (электрообессоливающую установку) для очистки от воды и солей. ЭЛОУ, используемые на НПЗ, принципиально не отличаются от подобных установок, используемых на нефтяных промыслах. Нефть подогревается до 100-120°С и подвергается воздействию напряжения порядка 30 кВ, в результате чего происходит отделение воды. Для более эффективного протекания процесса в сырьё добавляется деэмульгатор — вещество, способствующее разрушению эмульсии. Вода собирается внизу аппарата и удаляется, очищенная нефть поступает на установку атмосферно-вакуумной перегонки.
АВТ (атмосферно-вакуумная трубчатка) — одна из основных установок нефтеперерабатывающего завода. Она состоит из двух ректификационных колонн (атмосферной и вакуумной) и трубчатых печей, в которых осуществляется нагрев сырья.
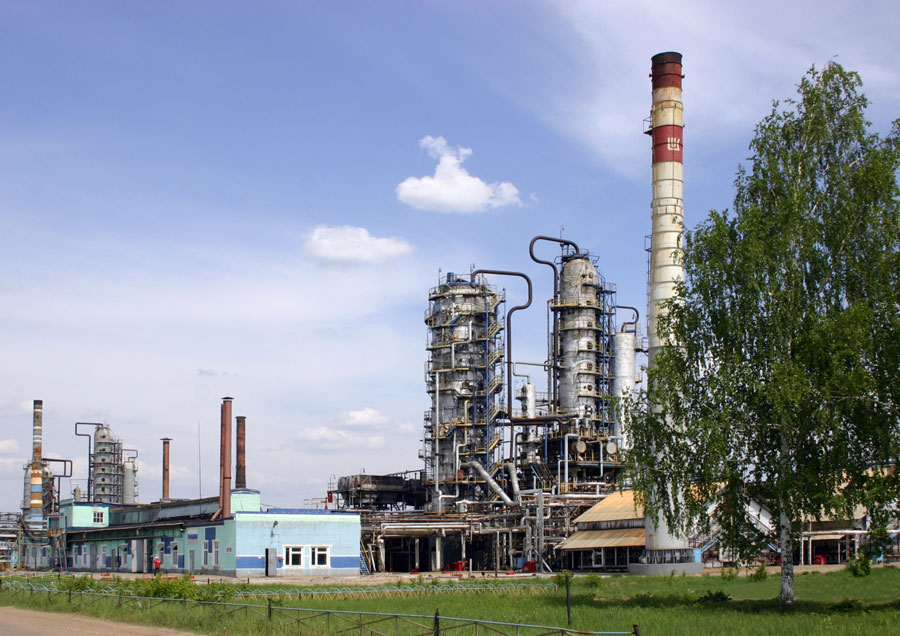
Процесс атмосферной перегонки предназначен для отбора светлых нефтяных фракций — бензиновой, керосиновой и лёгкой дизельной. Перегонка осуществляется при атмосферном давлении и температуре 300-360°С. Ректификационная колонна представляет собой цилиндрический вертикальный аппарат, внутри которого расположены несколько десятков устройств, внешне похожих на тарелки. Температура в колонне постепенно снижается от низа к верху, поскольку снизу колонна подогревается, а сверху осуществляется отбор тепла. Жидкость стекает по тарелкам вниз, поступает в зону более высокой температуры и постепенно испаряется. Одновременно поднимающийся снизу пар постепенно охлаждается и конденсируется на тарелках. В результате сверху колонны собирается бензиновая фракция в виде паров (температура кипения — до 180°С), ниже конденсируются керосиновая (180-240°С) и дизельная фракции (240-360°С), а в самом низу колонны остаётся мазут — смесь тяжёлых углеводородов. Светлые фракции, отбираемые в ходе атмосферной перегонки, составляют 40-60% исходного сырья.
Мазут, оставшийся после атмосферной перегонки, для дальнейшей переработки требуется разделить на составляющие фракции. Тяжёлые фракции, из которых состоит мазут, кипят при температуре выше 500°С, но нагревать сырьё сильнее 380 °С нельзя — при этом начнётся неуправляемое термическое разрушение углеводородов. Для снижения температуры кипения в вакуумной колонне при помощи насосов создаётся разрежение до 40-60 мм рт. ст. Это позволяет уменьшить температуру процесса до 360-380°С. В ходе вакуумной перегонки отбираются масляные фракции или вакуумный газойль (в зависимости от профиля завода), остатком является гудрон — наиболее тяжелые нефтяные углеводороды.
Фракции, выделенные в ходе первичной перегонки, не являются готовой продукцией и требуют дальнейшей переработки. К примеру, бензиновая фракция имеет октановое число всего около 60 единиц, к тому же все прямогонные фракции имеют высокое содержание соединений серы. В зависимости от характеристик исходного сырья, в прямогонной дизельной фракции может быть 0,2-2,0% серы, тогда как принятый в России Технический регламент ограничивает этот показатель на уровне 0,005% (топливо класса 4) и 0,001% (топливо класса 5). Для того, чтобы получить качественные товарные нефтепродукты, фракции первичной перегонки нужно подвергнуть различным превращениям на установках вторичной переработки.